How To Choose The Right End Mill Set?
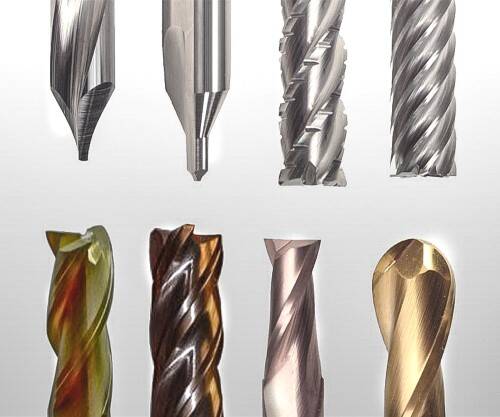
If you're running an operation that involves machining, whether it is a small CNC within the back of your garage, or an important manufacturing business, you have likely purchased a few last mill sets to satisfy your requirements.
You are probably aware that drill bits only be used in the direction of axial, while end mills for aluminum give you greater capabilities, allowing you to profile, trace and face. It means you have to make frequent changes to your tool when you work with pieces that require plunging, countersinking profile cutting, grooving, or chamfering. What would you do if we said there were ways to cut down on downtime and keep your spindle in good working order?
End mills are specifically designed for milling applications but can take on different roles. Based on the number of flutes and the geometry of the mill, they are able to be used for roughing, slotting, finishing, or high-efficiency machining. End mill sets often come with center-cutting heads that permit plunging cuts, as well as countersinks with chamfered edges to secure flush screws. When you wish for a full article on mill end bits, check out the post right here.
Choosing the right flat end mill will require you to establish the type of the work you'll work on. This allows you to narrow the tools you choose to purchase so that you purchase only mills that will see real use in the near future. Let's review the most important aspects to consider.
Materials
Before you choose the tools you will use, it is essential to be aware of the materials which you'll work with. Plastic behaves differently to steel which is why different machining strategies are needed. Before you purchase tools, it is important to think about the geometry, sharpness, as well as the mechanical properties of your tool. This can not only help improve accuracy and efficiency however, it will also save you time and money in the long run by prolonging the lifespan of your tools.
Flute count
Flutes are used to calculate the number of contact points your device will make with the material, and the efficiency of chip evacuation. For softer materials, a low flute count is preferable since it provides a better chip clearance and heat control. Finishing operations, however, will benefit from counts of flutes that are greater. A mill that has 5-14 flutes will produce superior results as well as a more polished surface.
Coating
When machining hardened steels, non-ferrous alloys, and hardwoods, you need tools with high-temperature refractory properties. Carbide end-mill sets can be used to stand up to extreme temperatures without losing their sharpness and the structural strength. This is an advantage when working with a large amount of material. It ensures that heat stays in check and does not compromise accuracy. Hardwoods are also able to be machined using an carbide coating as it makes it simpler to work with the material.
Conclusion:
When selecting your tools, it is important to think about the material you'll be working on and the particular requirements required for this particular task. If you're going to work with materials that are hard, ensure that your tools have high-temperature resistance capabilities. Additionally, take into consideration the options for coatings and how they might influence your process.
Maak jouw eigen website met JouwWeb