Cone Crusher Liners What To Consider And When To Change
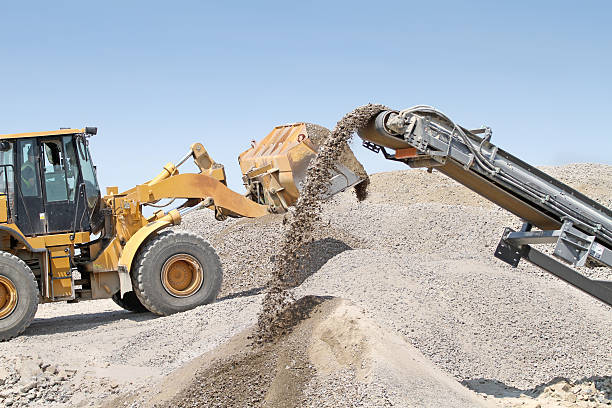
Cone Crushers were developed around a century ago to provide secondary, tertiary and even quaternary material reduction.
Cone Crushers are similar to other crushers that compress. They come with the crushing chamber or cavity, where the rock is crushed to a smaller size. Cone Crushers have a crushing chamber. This is the space between concaves and the mantle, which is the moving steel piece. Concaves and mantles are shielded from wear and tear by liners made of manganese that can be replaced.
What is the best cone crusher liner
A broad range of liners can accommodate coarse and fine feeds. However, the one you choose depends on several elements. The primary factor to consider when it comes to Cone Crusher Liners selection is the feed.
A properly graded feed must be utilized to crush the material. A well-graded feed should be:
90 to 90% of the feed opening on the closed side. Some people also look at the open side and select the less crowded one.
40%-60% at the middle
Closed-side Setting: 0-10%
You want to match the entire feed gradation, not only the feed size, to make sure you use the entire chamber. It is important to utilize the entire crushing chamber as is possible in order to achieve the reduction you need and the desired throughput.
The feed size of your plant as well as the output from the earlier crushing stage define the maximum feed size that gives the maximum cavity opening. The cavity opening should not be excessively large relative to the top size of your feed. Cavity openings that are larger than the feed size lead to poorly utilized reductions and liners.
If the feed size is not large enough then the bulk of the crushing occurs in the lowest portion of the cavity. This means that the bottom of the liners will wear away faster than the top liners. The output will decline due to the poor reduction ratio. At a minimal volume level the jaw crusher's power limit could be exceeded and bearing alignment problems can occur.
The bulk of wear on Mill Liners Foundry, occurs just before the parallel area (the narrowest space between the mantle and concaves where final crushing takes place). However, this wear can be increased if your feed is too small. It's possible to have a a bowled out pocket before the parallel zones.
However, feed sizes that are too small will cause the feed material to flow within the feed opening. This can lead to the liners wearing down faster. Because the feed opening has been covered, the production is reduced, and throughput is reduced. The output gradation is more coarse, and the final product will be slabby, not cubical. The volume limit is overrun at a minimum power draw.
Understanding the way your gradation is going to enter the crusher helps you to pick the most suitable Shredder Parts configuration necessary to achieve your production objectives. A good liner selection will provide you with a more effective tip, and also allow more flexibility to adjust other parameters like the closed-side setting.
Maak jouw eigen website met JouwWeb